If your Sub Zero ice maker is experiencing issues, check the water supply and temperature settings. Additionally, make sure the appliance is level and free of blockages.
Furthermore, regularly clean the condenser coils to prevent issues. If you’re experiencing trouble with your Sub Zero ice maker, a few simple troubleshooting steps can often resolve the issue. Proper maintenance, such as checking the water supply and temperature settings, can have a big impact on its performance.
It’s also important to ensure that the appliance is level and free of any blockages that could be impeding its function. Additionally, regular cleaning of the condenser coils can prevent many common issues. In this guide, we’ll explore these troubleshooting steps in detail, helping you to quickly identify and address any problems with your Sub Zero ice maker.
Common Sub Zero Ice Maker Problems
When it comes to Sub Zero ice makers, there are common issues that can arise, impacting the performance and quality of the ice produced. Identifying and troubleshooting these problems can help solve the issues effectively, ensuring your ice maker operates efficiently. Below are the most common Sub Zero ice maker problems you may encounter, along with troubleshooting tips to help get your ice maker back on track.
No Ice Production
If your Sub Zero ice maker is not producing any ice, it could be due to several reasons. Here are some troubleshooting tips to address this issue:
- Check the water supply to the ice maker to ensure it is connected and functioning properly.
- Inspect the water inlet valve for any blockages or malfunctions that may be hindering water flow.
- Verify that the freezer temperature is set to the appropriate level for ice production.
Ice Maker Leaking
Experiencing a leaking ice maker can be frustrating, but there are steps you can take to troubleshoot and resolve this issue:
- Inspect the water supply line for any signs of damage or leaks.
- Check the ice maker’s water inlet valve and ensure it is securely connected and not malfunctioning.
- Examine the ice maker’s drain system for clogs or obstructions that may be causing leaks.
Ice With Bad Taste Or Odor
When your Sub Zero ice maker produces ice with a bad taste or odor, it can impact the enjoyment of your beverages. Try these troubleshooting steps to improve the taste and odor of your ice:
- Clean the ice maker and its components regularly to prevent the accumulation of impurities that can affect ice quality.
- Replace the water filter in your ice maker to ensure the water used for ice production is clean and free from contaminants.
- Consider using a water treatment system to enhance the quality of the incoming water supply.
Checking For Basic Issues
If your Sub Zero ice maker is not functioning properly, it is important to start by checking for basic issues before diving into more complex troubleshooting. By addressing these basic problems, you may be able to quickly resolve the issue without the need for professional help. In this section, we will cover the three most common basic issues that can cause problems with your ice maker: power supply, water supply, and freezer temperature.
Power Supply
The first thing to check when troubleshooting your Sub Zero ice maker is the power supply. Ensure that the ice maker is properly connected to a functioning power source. Here’s what to look for:
- Check if the power cord is securely plugged into the outlet.
- Test the outlet by plugging in another appliance or device to confirm if it’s working.
- Make sure that the power switch on your ice maker is turned on, if applicable.
By verifying the power supply, you can eliminate a potential source of the problem.
Water Supply
The second basic issue to check is the water supply for your Sub Zero ice maker. Without a steady flow of water, your ice maker will not be able to produce ice. Follow these steps to ensure proper water supply:
- Verify that the water supply valve, typically located behind the refrigerator, is fully open.
- Inspect the water line for any kinks or leaks that could be obstructing the water flow.
- If your ice maker has a water filter, check if it needs replacement or cleaning according to the manufacturer’s instructions.
Addressing any problems with the water supply will improve the chances of your ice maker functioning correctly.
Freezer Temperature
The third basic issue to consider is the freezing temperature of your freezer. The freezer must maintain an adequate temperature for the ice maker to operate efficiently. Follow these guidelines to check the freezer temperature:
- Ensure that the freezer temperature is set to a recommended level, usually between 0 and 5 degrees Fahrenheit (-18 to -15 degrees Celsius).
- Use a thermometer to measure the actual temperature inside the freezer and compare it to the desired setting. Adjust if necessary.
By maintaining the correct freezer temperature, you can maximize the ice maker’s performance and prevent freezing or melting issues.
Cleaning And Maintenance
Ensure your Sub Zero ice maker runs smoothly by regularly performing cleaning and maintenance. Keep the machine free from debris and thoroughly clean the water supply line to troubleshoot any issues. Regular maintenance can help extend the lifespan of your Sub Zero ice maker.
Clearing Ice Build-up
If you notice that your Sub Zero ice maker is not producing ice or the ice cubes are coming out small or malformed, it could be due to ice build-up. Over time, the water that fills the ice maker can freeze onto the evaporator, creating a layer of ice that prevents proper ice production. To solve this issue, follow these simple steps to clear the ice build-up:
- Turn off the ice maker by flipping the switch or unplugging it from the power source.
- Remove any ice cubes or ice trays from the ice maker.
- Locate the ice maker’s evaporator cover and unfasten any screws or clips holding it in place.
- Gently lift or pull out the evaporator cover to expose the evaporator coils.
- Using a hairdryer set on low heat, carefully melt the ice build-up on the evaporator coils. Be sure to keep the hairdryer at least six inches away from the coils to prevent damage.
- Once all the ice has melted, replace the evaporator cover and secure it with the screws or clips.
- Finally, turn on the ice maker and check if it starts producing ice normally. If not, you may need to consult a professional technician to further diagnose the issue.
Cleaning Filter
Regular cleaning of the filter is essential to maintain the performance and efficiency of your Sub Zero ice maker. The filter helps to remove impurities from the water, ensuring your ice is clean and safe to consume. Follow these steps to clean the filter:
- Locate the water filter of your Sub Zero ice maker. It is typically located in the upper left corner of the ice maker compartment.
- Turn off the ice maker and close the water shut-off valve to prevent any water flow.
- Gently twist the filter counterclockwise to remove it from its housing.
- Rinse the filter under running water to remove any debris or sediment. You can also use a soft brush to scrub away stubborn dirt.
- Once the filter is clean, reinstall it by twisting it clockwise into the housing.
- Open the water shut-off valve and turn on the ice maker. Allow it to run for a few minutes to flush out any air or particles that may be present.
Sanitizing Ice Maker
Sanitizing your Sub Zero ice maker periodically is important to ensure that the ice it produces is free from bacteria or contaminants. Follow these steps to sanitize your ice maker:
- Empty the ice maker of any ice cubes or ice trays.
- Mix a solution of warm water and mild dish soap.
- Dip a clean cloth or sponge into the soapy water and wipe down the interior surfaces of the ice maker, including the ice tray and dispenser.
- Rinse the cloth or sponge with clean water and wipe down the surfaces again to remove any soap residue.
- For added sanitization, you can use a mixture of one part vinegar and two parts water. Apply this solution to the interior surfaces of the ice maker and let it sit for a few minutes before wiping it clean.
- Once the ice maker is clean and sanitized, leave the door or flap open to allow for proper drying.

Credit: partsfe.com
Inspecting Components
Inspecting Components is an essential troubleshooting step when dealing with Sub Zero ice maker issues. By examining each component carefully, you can identify the problem and take appropriate action to fix it. In this section, we will discuss three crucial components that often require inspection: Ice Maker Assembly, Water Inlet Valve, and Ice Mold Thermostat.
Ice Maker Assembly
The Ice Maker Assembly is the crucial part responsible for producing ice cubes. A thorough inspection of this component can reveal common problems like clogged water lines, damaged fill cups, or faulty motors. Here are a few steps to inspect the Ice Maker Assembly:
- Check for clogs: Examine the water lines connected to the ice maker, ensuring there are no blockages. Clear any obstructions if found.
- Inspect the fill cups: These cups allow water to enter and freeze into ice cubes. Look for cracks or chips in the cups that may affect the ice-making process.
- Test the motor: Turn the ice maker on and observe if the motor is running smoothly. Unusual noises or a motor that fails to turn could indicate a problem.
Water Inlet Valve
The Water Inlet Valve controls the flow of water to the ice maker. If there are issues with ice production, it’s important to inspect this component. Follow these steps to examine the Water Inlet Valve:
- Check for leaks: Inspect the valve for any signs of leakage. Even a small leak can disrupt the ice-making process and cause performance issues.
- Test the valve: Use a multimeter to measure the continuity of the valve. If there is no continuity, it may need to be replaced.
- Clean the valve: Sediments and mineral deposits can accumulate over time, affecting the valve’s functionality. Clean the valve thoroughly to ensure proper water flow.
Ice Mold Thermostat
The Ice Mold Thermostat regulates the temperature inside the ice maker, ensuring the ice cubes freeze correctly. If your ice maker is producing improperly formed or slowly freezing ice, examining the Ice Mold Thermostat is vital. Here’s how to inspect it:
- Inspect the wiring: Check for loose or damaged wires connected to the thermostat. Replace any faulty wiring if necessary.
- Test the thermostat: Using a multimeter, measure the thermostat’s resistance at different temperature settings to verify its functionality.
- Adjust the temperature: If the thermostat is adjustable, ensure it is set to the correct temperature for proper ice cube formation.
Troubleshooting Electrical Problems
Sub Zero ice maker troubleshooting is essential for resolving electrical problems. By following expert tips and guidelines, users can pinpoint issues affecting their ice maker’s performance and ensure efficient functionality. Find step-by-step solutions to address common malfunctions and understand the intricate workings of your Sub Zero ice maker.
Introduction:
When it comes to troubleshooting electrical problems with your Sub Zero ice maker, it’s important to have a systematic approach. Electrical issues can cause your ice maker to malfunction or stop working altogether. In this section, we’ll explore three key areas to investigate: testing the power source, checking wiring connections, and assessing the control module. By following these troubleshooting steps, you’ll be able to identify and resolve electrical problems with your Sub Zero ice maker.
Testing Power Source:
To start troubleshooting electrical problems with your Sub Zero ice maker, it’s crucial to ensure that the power source is working correctly. Here’s how you can test the power source:
- Check if the ice maker is plugged into a working electrical outlet. Ensure that the outlet is supplying power by using a multimeter or plugging in another appliance.
- If the outlet is functioning properly, verify that the circuit breaker or fuse connected to the ice maker is not tripped or blown. Reset the breaker or replace the fuse if necessary.
- Inspect the power cord for any visible signs of damage or wear. If the cord is damaged, it may need to be replaced.
Checking Wiring Connections:
Next, it’s essential to examine the wiring connections in your Sub Zero ice maker. Loose or faulty connections can cause electrical issues. Follow these steps to check the wiring connections:
- Unplug the ice maker from the power source before inspecting the wiring.
- Carefully examine each wire connection for any signs of looseness or corrosion. Secure any loose connections by tightening them with a screwdriver.
- If you notice any damaged or frayed wires, they will need to be replaced. Consult a professional technician or refer to the user manual for instructions on replacing the wiring.
Assessing Control Module:
The control module in your Sub Zero ice maker is responsible for regulating the ice-making process. If there are electrical problems with the control module, it can disrupt the ice production. Here’s how you can assess the control module:
- Locate the control module, usually located near the front or back of the ice maker.
- Inspect the module for any visible signs of damage, such as burnt components or loose connectors.
- If you suspect a malfunctioning control module, it may need to be replaced. Contact a professional technician who has experience with Sub Zero ice makers or refer to the user manual for guidance.
By systematically troubleshooting the electrical problems in your Sub Zero ice maker, you can identify and resolve any issues that may be hindering its performance. Remember to always follow safety precautions and consult a professional technician if needed. With the right troubleshooting steps, you can enjoy a fully functional ice maker in no time.
Addressing Water Supply Issues
Sub Zero ice makers are known for their reliability, but occasionally, users may encounter water supply issues affecting ice production. A key factor in troubleshooting these issues is addressing water supply problems. In this section, we’ll discuss various troubleshooting steps to address water supply issues effectively.
Examining Water Line
Inspect the water line for any kinks, bends, or blockages that may restrict water flow to the ice maker. Ensure the water line is properly connected and not damaged.
Filter Replacement
Regularly replace the water filter to ensure clean and unrestricted water flow to the ice maker. A clogged or old filter can hinder water supply and affect ice production.
Adjusting Water Pressure
Check the water pressure to ensure it meets the recommended levels for the Sub Zero ice maker. Improper water pressure can lead to inadequate water supply, impacting ice production.
Dealing With Ice Quality Problems
When it comes to enjoying refreshing beverages, the quality of ice plays a crucial role. Subpar ice quality can affect the taste and odor of your drinks. If you’re facing ice quality problems with your Sub Zero ice maker, it’s essential to address these issues promptly. Identifying contamination sources, improving ice taste, and eliminating odors are key steps in troubleshooting ice quality problems. Let’s dive into these solutions to ensure your ice maker delivers pristine ice for your beverages.
Identifying Contamination Sources
If you notice unusual tastes or odors in your ice, it’s crucial to identify potential contamination sources. Check for these possible sources of contamination:
- Dirty Ice Bin: Regularly clean the ice bin to remove any accumulated debris or molds. Use a mild soap and water solution followed by a thorough rinse.
- Water Supply: Test the water supply feeding into the ice maker for impurities. Install water filters if necessary to ensure clean water for ice production.
- Unsealed Food Items: Keep uncovered foods away from the ice maker to prevent cross-contamination.
- Untidy Freezer: Maintain a clean freezer environment to prevent the transfer of unwanted flavors to the ice.
Improving Ice Taste
Enhancing the taste of your ice is essential for a delightful drinking experience. Consider these steps to improve the taste of your ice:
- Regular Cleaning: Clean the ice maker components, including the ice bin, water lines, and ice mold, to remove any buildup affecting the ice taste.
- Filtered Water: Use a high-quality water filter to ensure the water used for ice production is free from impurities that could alter the taste.
- Ice Sanitization: Utilize ice machine cleaner to sanitize the internal components and eliminate any lingering flavors impacting the ice taste.
Eliminating Odors
Unpleasant odors in ice can significantly impact the enjoyment of your beverages. Take these steps to eliminate odors from your ice:
- Vinegar Rinse: Use a solution of water and vinegar to clean the ice maker, effectively removing any odors accumulated within the system.
- Regular Maintenance: Perform routine maintenance to keep the ice maker clean and odor-free, minimizing the chance of unpleasant odors affecting the ice.
- Proper Storage: Store any food items in the freezer in sealed containers to prevent their odors from seeping into the ice.

Credit: boxappliance.com
Understanding Freezer Conditions
Gain a deeper understanding of freezer conditions by troubleshooting common issues with Sub Zero ice makers. Explore solutions to ensure your freezer functions optimally.
To effectively troubleshoot a Sub Zero ice maker, it is crucial to understand the conditions within the freezer. Factors such as the optimal freezer temperature, air circulation, and the impact of overstuffing can significantly affect the ice maker’s performance and functionality. Let’s delve into each of these aspects to gain a deeper understanding.Optimal Freezer Temperature
Maintaining the correct freezer temperature is essential for the Sub Zero ice maker to operate efficiently. The optimal temperature range for the freezer is between 0°F and 5°F (-18°C and -15°C). A temperature that is too warm can lead to slow ice production, while a temperature that is too cold may result in ice clumping or the ice maker failing to work altogether.Air Circulation In Freezer
Proper air circulation within the freezer is vital for the ice maker’s performance. Adequate airflow prevents the buildup of excess frost, which can impair the ice maker’s functioning. To ensure optimal air circulation, avoid blocking the vents or obstructing the fan inside the freezer. Keeping the vents clear allows cold air to circulate freely, maintaining the desired temperature and enabling the ice maker to function optimally.Impact Of Overstuffing
Overstuffing the freezer can have a negative impact on the Sub Zero ice maker. When the freezer is overloaded, it restricts proper airflow, causing temperature imbalances and hindering the ice maker’s effectiveness. Additionally, overcrowding the freezer can lead to excessive frost buildup, further impeding the ice-making process. It is advisable to organize items within the freezer, ensuring proper spacing between them to promote adequate airflow and optimize ice production. Understanding these crucial freezer conditions is the first step towards troubleshooting a Sub Zero ice maker. By maintaining the optimal freezer temperature, facilitating proper air circulation, and avoiding overstuffing, you can ensure the smooth operation of your ice maker and enjoy a continuous supply of refreshing ice. Take a moment to assess the conditions of your freezer and make any necessary adjustments to enhance the performance of your Sub Zero ice maker.Replacement And Repair Options
Experiencing issues with your Sub Zero ice maker can be frustrating, but fortunately, there are several replacement and repair options available to get your ice maker back up and running in no time. Whether you prefer to replace specific components, enlist the help of professional repair services, or attempt a DIY repair, there are solutions tailored to your needs.
Replacing Ice Maker Components
If you’ve identified a specific component causing trouble with your Sub Zero ice maker, replacing that component may be a viable solution. This option allows you to address the problem directly without incurring the expense of professional repair services. Here are a few common components that can often be easily replaced:
Component | Symptoms | Replacement Process |
---|---|---|
Water Inlet Valve | No water flow or inadequate water supply | 1. Turn off the ice maker’s power supply 2. Disconnect the water supply line 3. Unscrew the old water inlet valve 4. Install the new water inlet valve 5. Reconnect the water supply line 6. Turn on the power supply |
Ice Maker Control Module | Inconsistent ice production or no ice at all | 1. Unplug the ice maker 2. Locate and remove the control module 3. Replace it with a new control module 4. Plug in the ice maker |
Ice Maker Motor | Noisy operation or failure to dispense ice | 1. Disconnect the ice maker’s power supply 2. Remove the ice maker from its mounting 3. Replace the faulty motor with a new one 4. Reinstall the ice maker and reconnect the power supply |
Professional Repair Services
If you’re facing complex issues or unsure about replacing components yourself, seeking professional repair services is highly recommended. These experts have the know-how and the necessary tools to diagnose and fix a wide range of problems with your Sub Zero ice maker. Hiring a professional offers the advantage of their expertise and the convenience of not having to troubleshoot the issue on your own. To find a reliable repair service, check with the manufacturer or consult online directories for trusted repair technicians in your area.
Considerations For Diy Repair
For those who are inclined towards DIY repairs, there are some considerations to keep in mind. While DIY repairs can save you money, it is essential to have a basic understanding of the ice maker’s components and potential issues. Additionally, be sure to follow safety precautions and refer to manufacturer instructions or reputable online resources for guidance. It’s important to note that attempting a DIY repair without proper knowledge or tools can worsen the problem or even cause further damage. If you feel unsure about your capabilities, it’s best to seek professional assistance to prevent any complications.
Preventive Measures
To keep your Sub Zero ice maker running smoothly, it’s essential to take preventive measures. By following these tips, you can avoid common issues and ensure that your ice maker consistently produces ice of the highest quality.
Regular Cleaning Schedule
Regularly cleaning your Sub Zero ice maker is vital to its proper functioning. This prevents the build-up of mineral deposits, mold, and bacteria that can affect the taste and quality of the ice. Establishing a cleaning schedule and sticking to it will help maintain your ice maker’s efficiency.
To clean the ice maker, start by turning off the appliance and disconnecting it from the power source. Remove the ice storage bin and any remaining ice cubes. Prepare a mixture of warm water and mild dish soap. Use a soft cloth or sponge to wipe down the interior surfaces, including the ice chute and water dispenser. Rinse thoroughly and dry everything before reassembling the ice maker.
Monitoring Ice Production
Monitoring the ice production of your Sub Zero ice maker is essential to catch any issues early on. Pay attention to the quantity and quality of the ice being produced. If you notice a significant decrease in ice production or if the ice is smaller than usual or contains impurities, it’s a sign that something may be wrong.
Regularly inspect the water supply lines to ensure they are properly connected and free from any kinks or blockages. Additionally, check the ice maker’s temperature settings to ensure they are at the recommended levels for optimal ice production.
Maintaining Proper Freezer Conditions
Maintaining the freezer conditions is crucial for the smooth operation of your Sub Zero ice maker. Ensure that the freezer temperature is set to the recommended level, typically between -2°F and 2°F (-19°C and -17°C). This will help ensure that the ice maker functions at its best.
In addition, avoid overloading the freezer with food items, as this can restrict airflow and affect the ice maker’s performance. Regularly clean the freezer compartment to prevent any ice or debris from obstructing the ice maker’s operation.
By following these preventive measures of regular cleaning, monitoring ice production, and maintaining proper freezer conditions, you can prolong the lifespan of your Sub Zero ice maker and enjoy an uninterrupted supply of ice.
Professional Assistance
When it comes to troubleshooting your Sub Zero ice maker, sometimes you may find yourself in need of professional assistance. While there are troubleshooting steps you can take on your own, enlisting the help of experts can save you time and ensure a proper diagnosis and solution to your ice maker woes.
Contacting Sub Zero Service Center
If you are experiencing issues with your Sub Zero ice maker, one of the best ways to get professional assistance is by contacting the Sub Zero service center. They have a team of trained technicians who specialize in Sub Zero appliances and can provide you with the expertise you need to get your ice maker back up and running smoothly.
Seeking Expert Advice
If you prefer seeking expert advice outside of the Sub Zero service center, there are other options available. You can reach out to independent appliance repair companies that have experience with Sub Zero appliances. They can offer valuable insights and solutions based on their expertise in dealing with similar ice maker problems.
Warranty Coverage
Before seeking professional assistance, it’s important to check your warranty coverage. If your Sub Zero ice maker is still under warranty, you may be eligible for free repairs or replacement parts. Contacting the Sub Zero service center or referring to your warranty documentation will provide clarity on what is covered and how to proceed with getting professional assistance.
In conclusion, when facing troubleshooting issues with your Sub Zero ice maker, seeking professional assistance is a wise decision. Whether you reach out to the Sub Zero service center or seek advice from independent experts, their knowledge and experience can help resolve your ice maker problems efficiently, ensuring your appliance continues to produce refreshing ice for your needs.
Ensuring Long-term Ice Maker Performance
Successful troubleshooting for your Sub Zero ice maker is crucial to maintaining long-term performance. By focusing on proper use and care, upgrading ice maker technology, and future maintenance planning, you can effectively maximize the lifespan and efficiency of your ice maker.
Proper Use And Care
To ensure the longevity of your Sub Zero ice maker, it’s essential to follow proper use and care guidelines. This includes regular cleaning of the ice maker and the surrounding area. Additionally, it’s important to use the ice maker as intended, avoiding overloading it or using it for purposes other than making ice.
Upgrading Ice Maker Technology
As technology advances, it’s worth considering upgrading your ice maker to take advantage of the latest features and improvements. Newer models may be more energy-efficient and have enhanced performance capabilities, ultimately contributing to long-term ice maker reliability.
Future Maintenance Planning
Implementing a plan for future maintenance is essential to sustaining the performance of your ice maker. This includes scheduling regular maintenance checks and staying informed about potential updates or upgrades that can further enhance the ice maker’s efficiency.
Impact Of Environmental Factors
The impact of environmental factors on sub-zero ice maker troubleshooting can have significant consequences. From temperature fluctuations to water quality issues, these external elements play a crucial role in the proper functioning of the appliance. Understanding and addressing these factors is essential for effective troubleshooting and maintenance.
Temperature Fluctuations
Temperature fluctuations can greatly impact the performance of your Sub Zero ice maker. The machine relies on consistently cool temperatures to efficiently freeze the water and produce ice. Extreme temperatures, whether they are too high or too low, can lead to various issues and hinder the ice-making process.
If the ambient temperature is too high, the ice maker may struggle to reach the desired freezing point, resulting in slow ice production or no ice at all. On the other hand, if the temperature is too low, the machine might overcompensate by freezing the water excessively, causing the ice to become overly hard, and potentially damaging the internal components in the process.
Humidity Levels
Humidity levels also play a crucial role in the performance of your Sub Zero ice maker. High humidity can affect how quickly the ice freezes and how smoothly it is released from the ice maker. Excess moisture in the air can lead to ice cubes clumping together, making it difficult to dispense them.
Conversely, low humidity levels can cause the ice to evaporate or melt rapidly once it is produced. This can result in an insufficient supply of ice, especially in warm environments where the ice maker has to work harder to keep up with the demand. It is important to maintain optimal humidity levels to ensure consistent ice production and prevent any potential issues.
External Contaminants
External contaminants can also have a significant impact on the functionality of your Sub Zero ice maker. Dust, dirt, and other particles can find their way into the machine, clogging the various components responsible for ice production. This can lead to reduced ice output, slow ice production, or even complete failure of the ice maker.
Furthermore, chemicals or substances like mineral deposits in the water supply can accumulate over time, affecting the taste and quality of the ice. Regular maintenance and cleaning of the ice maker can help prevent the buildup of external contaminants and ensure optimal performance.
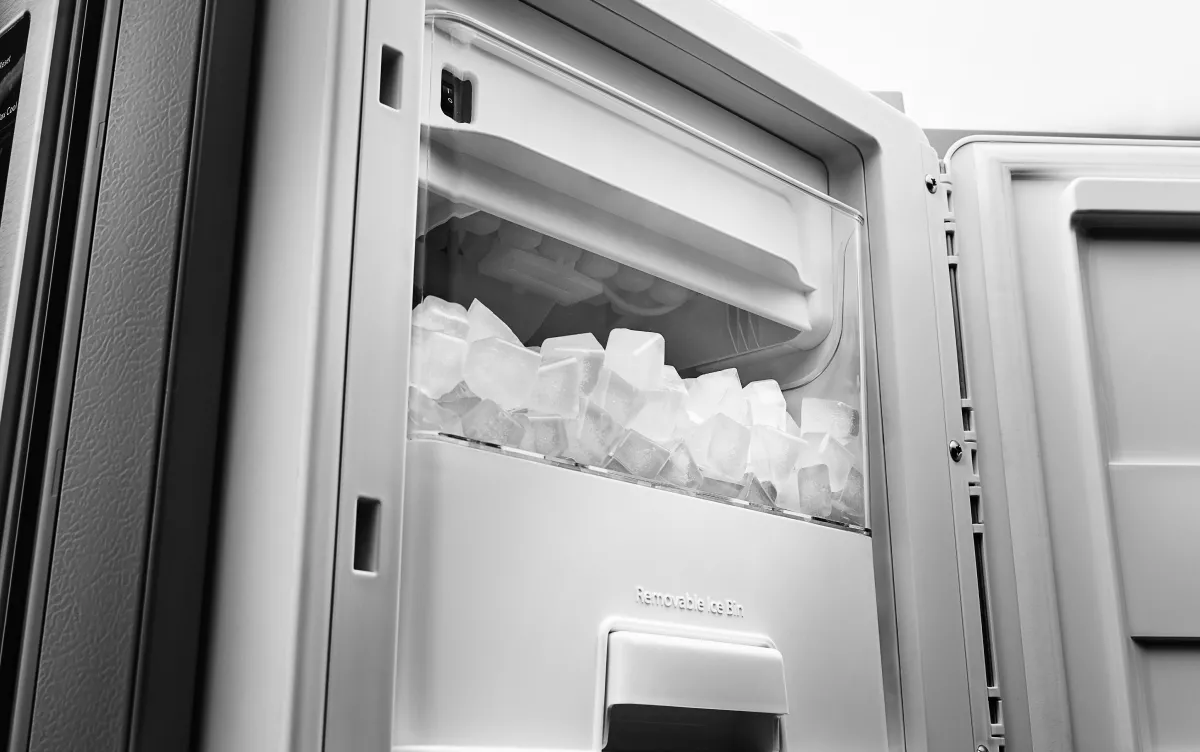
Credit: www.kitchenaid.com
Maintaining Ice Maker Efficiency
Maintain the efficiency of your Sub Zero ice maker by troubleshooting common issues. Keep your ice maker running smoothly for ice-cold refreshments with these simple tips and tricks.
Maintaining Ice Maker Efficiency Evaluating Energy Consumption When it comes to maintaining the efficiency of your Sub Zero ice maker, one crucial aspect to consider is its energy consumption. By evaluating the energy usage of your ice maker, you can identify any potential issues and take steps to optimize its performance. To evaluate energy consumption, start by examining the power consumption specifications provided by the manufacturer. This information can usually be found in the user manual or on the manufacturer’s website. Compare the specifications to your actual energy bills to determine if there are any discrepancies that may indicate a problem. Efficient Ice Production Techniques Efficient ice production techniques can significantly contribute to the overall efficiency of your Sub Zero ice maker. By following these techniques, you can ensure a consistent and reliable supply of ice while minimizing energy consumption. 1. Regularly clean and maintain your ice maker: – Clean the ice maker and its components according to the manufacturer’s instructions. – Remove any built-up mineral deposits or ice accumulations that can hamper performance. – Check and replace any worn-out or damaged parts. 2. Optimize ice production settings: – Adjust the ice production settings based on your actual needs. – A higher production rate may lead to increased energy consumption, so find the optimal balance. 3. Keep the ice maker well-insulated: – Ensure the ice maker is properly insulated to prevent heat transfer. – Check the door seal to make sure it is tightly closed, reducing temperature fluctuations and energy loss. 4. Use filtered water: – Filtering the water before it enters the ice maker can prevent mineral deposits and prolong its lifespan. – It can also enhance the appearance and taste of the ice produced. Eco-Friendly Practices In addition to efficient ice production techniques, incorporating eco-friendly practices can help reduce the environmental impact of your Sub Zero ice maker. By following these practices, you can contribute to a greener and more sustainable future. 1. Recycle ice melt water: – Instead of letting the melted ice water go to waste, consider using it for other purposes like watering plants or cleaning. 2. Opt for energy-saving mode: – If your ice maker has an energy-saving mode, enable it to reduce power consumption during idle periods. 3. Consider alternative ice sources: – Depending on your needs, you may want to explore alternatives to your ice maker, such as using ice trays or purchasing bagged ice from a local store. By evaluating energy consumption, implementing efficient ice production techniques, and adopting eco-friendly practices, you can maintain the peak efficiency of your Sub Zero ice maker. Not only will this ensure a steady supply of fresh ice, but it will also contribute to reducing energy consumption and promoting sustainability.Conclusion And Final Tips
After performing the troubleshooting steps and maintaining your Sub Zero ice maker, following these final tips can help ensure its continuous and efficient performance. Let’s dive into the summary of troubleshooting steps, key maintenance guidelines, and tips for ensuring a constant ice supply.
Summary Of Troubleshooting Steps
If you’ve encountered issues with your Sub Zero ice maker, following the troubleshooting steps outlined in this guide can help identify and resolve the issues. By cleaning the condenser, checking the water supply, and inspecting the ice maker assembly, you can address common problems and restore optimal functionality.
Key Maintenance Guidelines
To maintain the efficiency of your Sub Zero ice maker, regularly cleaning the condenser, inspecting the water supply line for leaks or blockages, and replacing the water filter are key maintenance tasks. Periodically defrosting the ice maker and ensuring proper ventilation around the unit can also contribute to its longevity and performance.
Ensuring Continuous Ice Supply
To ensure a steady supply of ice, it’s essential to regularly monitor the ice production, keep the freezer temperature consistent, and promptly address any issues with ice quality or production. By adhering to the maintenance guidelines and promptly addressing any performance issues, you can ensure a continuous and reliable ice supply for your needs.
Conclusion
To troubleshoot your Sub Zero ice maker effectively, follow these simple steps. Start by checking the water supply line, ensuring it is properly connected and free from any obstructions. Next, inspect the inlet valve and clean if necessary. Don’t forget to check the water filter and replace if needed.
Lastly, verify the temperature settings to ensure optimal ice production. By following these troubleshooting tips, you’ll be able to enjoy a fully functioning Sub Zero ice maker once again.